ELORA – A house made of hemp and limestone is a healthy home that will last longer, says Paul Flach.
That’s why the Elora resident is building a hemp house for his family.
The process is simple – mix one part water, one part limestone, and one part sheared hemp shives (the woody stem of the plant). Then, shovel the mixture into forms for the walls and ceiling, tamp it down, and let it cure.
Houses made of hemp and limestone are resistant to mold, “termite proof, rodent proof, and highly sound proof,” Flach said – and the limestone is antiseptic.
The materials regulate humidity by pushing moisture out if a house is too humid, and pulling it in if it’s too dry.
According to a review of hemp concrete published in the Journal of Cleaner Production, hemp concrete is carbon negative with “excellent moisture buffer capability,” and people have been cultivating hemp since 8,000 BCE.
Flach said hemp is an “industrial strength product” that can be grown at high volumes with high yields, while the plant replenishes the soil it grows in. He said high-level silicates make hemp more durable than other plants.
Flach is confident a house made of hemp and limestone can last 500 years.
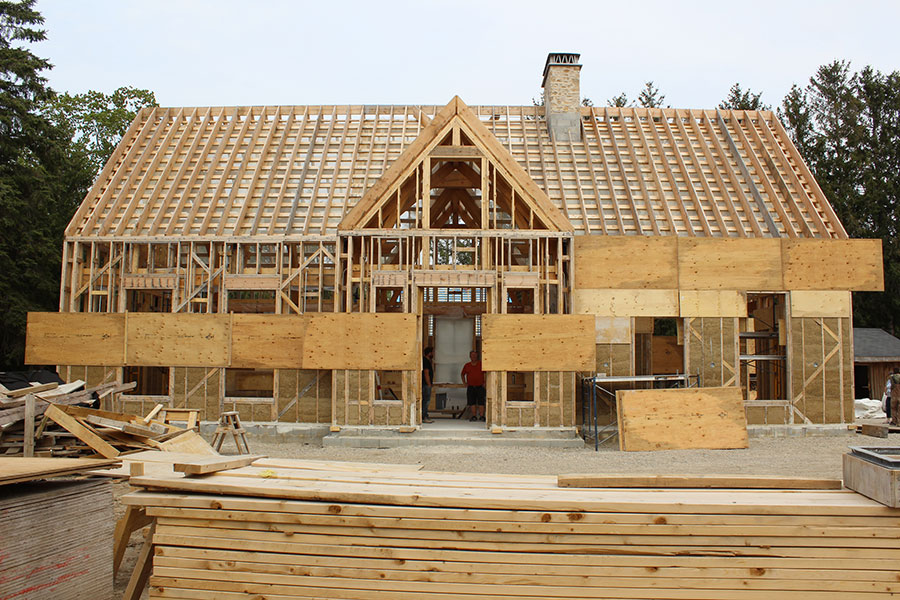
Under construction – This house in Elora is being constructed with walls made of a mixture of hemp, limestone and water.
The limestone in the mix adds to the durability, and unlike Portland cement that degrades over time, “lime gets harder and stronger,” Flach noted.
Inside a building made of hemp and limestone concrete, like the addition Flach built in his backyard, the “air is always clean smelling – that’s not the hemp, that’s the lime.
“You can tell the air quality is perfect,” Flach said, noting his concern about the impact that off-gassing in “synthetic homes” has on people’s health.
Off-gassing is when materials release chemical gasses that cause some people irritation or allergic reactions.
According to the Northeast Sustainable Energy Association, off-gassing is not an issue with concrete made from hemp because it is natural and non-toxic.
Flach said most people have “forgotten about the benefits of lime,” which can purify air by sequestering carbon and odors.
And unfortunately hemp, he said, is “stigmatized as a subculture,” which hampers the industry.
However, in recent years, it seems that stigma is waiving as “people are realizing the sophistication of this product,” he noted.
Flach is building his home with support from Stew Oliver, an “expert on hemp homes” with experience building them and teaching workshops across the continent.
Building a hemp house takes longer than building with other materials, and is “more expensive than your typical house,” but Flach said this is because hemp is still considered a niche product.
He is confident demand will continue to increase, leading to the price of hemp dropping significantly.
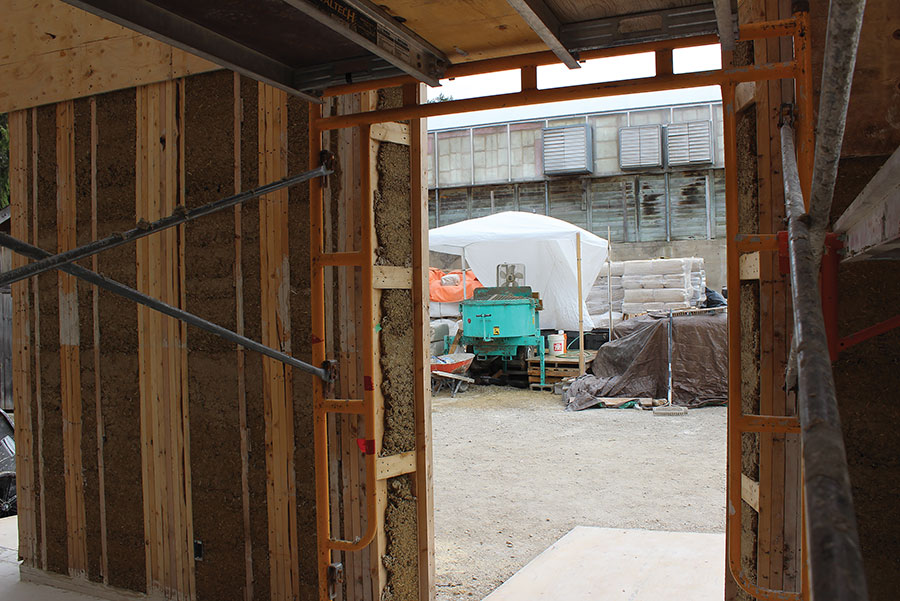
Curing process – The mixture of hemp, limestone and water is currently being shoveled into frames and then will cure for three weeks.
“The hemp itself to grow is very cheap,” Flach noted.
Building with hemp requires an alternate building application as hemp is not included in most building codes.
“We provided a really good case” in a permit application, Flach said, “and put a lot of money into having engineers study this.
“Now that we have done all that groundwork, we can help others build that case to make that application,” he said.